GIKEN LTD. (Head Office: Kochi-shi, President and CEO: Atsushi Ohira) and GIKEN SEKO CO., LTD. (Head Office: Kochi-shi, President and CEO: Akihiro Nishigawa) conducted on-site verification of iNAVILINK™ (autonomous operation) and G-Lab Vision (remote support)—digital transformation technologies that allow autonomous operation of press-in piling at remote locations—at the project for the construction of countermeasures against storm surges at Usa Port in Kochi Prefecture. These technologies provide innovative solutions to social issues such as the aggravating reduction of workforce in the construction industry. Going forwards, further feedback from construction sites will be collected to perfect these technologies and seek early commercialisation.
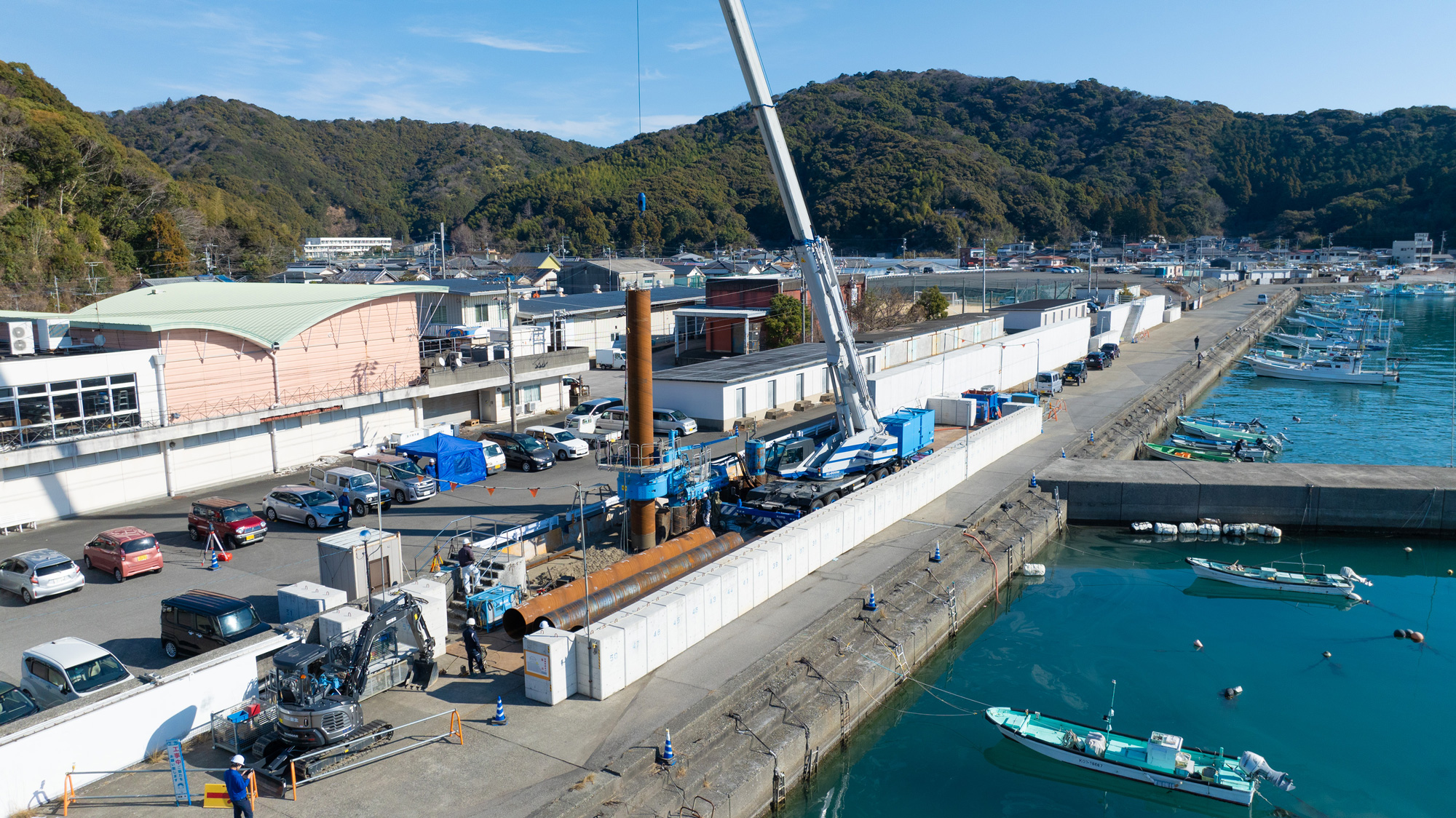
■ Regarding On-site Verification
Overview of Construction
GIKEN SEKO used the tubular pile rotary cutting press-in method Gyropress MethodTM to press in 19 steel tubular piles and build the foundation of a seawall that serves as a countermeasure against storm surges. Out of these piles, piling was carried out using iNAVILINKTM for 13 piles and G-Lab Vision for five piles.
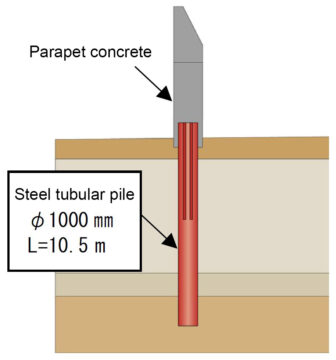
Prepared by GIKEN LTD. based on data supplied from Kochi Prefecture Civil Engineering Department Central West Civil Engineering Office
Equipment | Rotary cutting press-in machine for tubular piles GYRO PILERTM F401-G1200 |
---|---|
Specification of Pile Elements | 19 steel tubular piles (diameter of 1,000mm and length of 10.5m) |
Press-in Construction Period | January 26 to February 1, 2024 |
Technologies Verified, Scope of Verification, and Results
➤ Technology Verified (1): iNAVILINKTM (autonomous operation)
This is a system that can conduct accurate press-in according to the planned location and depth under autonomous operation, where the press-in machine collaborates with the pile installation quality system Implant NAVI™* to assess pile displacement and inclination.
This allows an increase in the automation rate of the press-in process to approximately 65% from the previous rate of approximately 35%. An improvement in labour productivity is expected, with one less person required due to the reduction of workload.
* Reference: Website of GIKEN (https://www.giken.com/en/products/ict/implantnavi/)
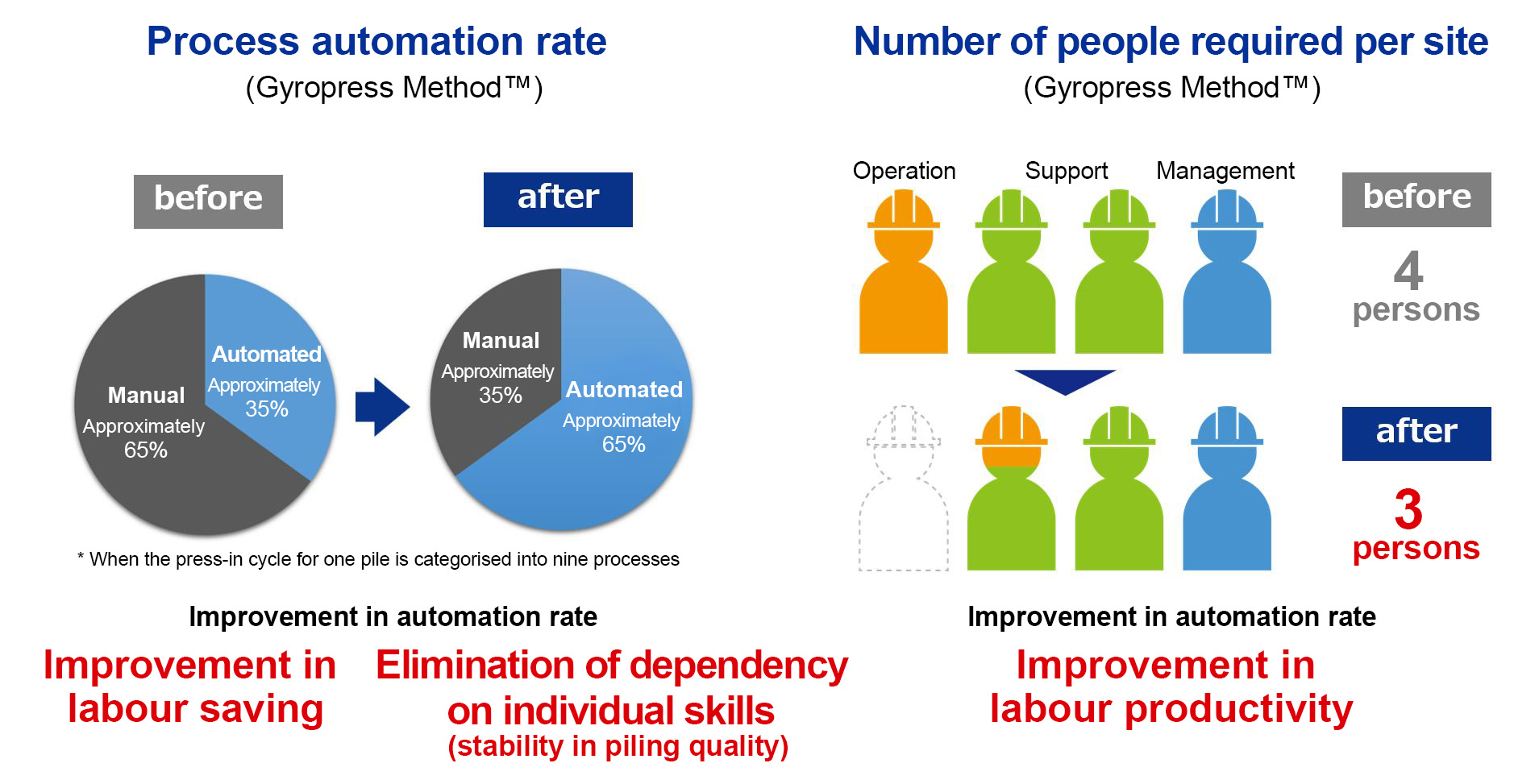
➤ Scope of Verification and Results (1): Piling efficiency and quality during autonomous operation
The results were as expected, confirming the same or better level of construction progress as past methods even though the workload is lower. In addition, regarding the piling quality of the pressed-in piles, all piles cleared the standards (standard height, deviation, and inclination) stipulated by the Ministry of Land, Infrastructure, Transport and Tourism. Going forwards, the technology will be further improved to meet the higher in-house standards of GIKEN.
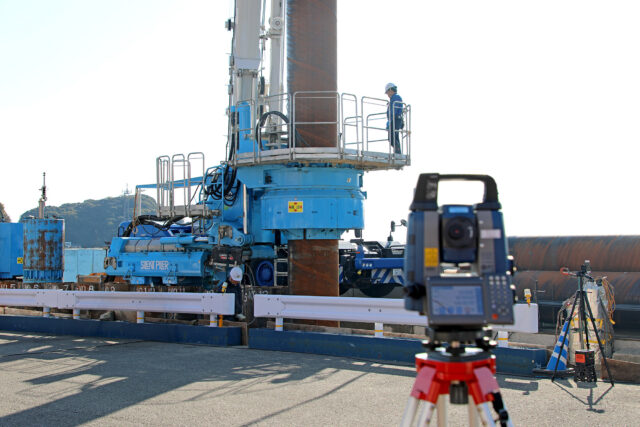
➤ Technology Verified (2): G-Lab Vision (remote support and simulation)
This system creates a digital twin* using 3D model data and real-time measurement data of the press-in site (machinery, piles, and site environment). It allows remote piling and simulation while confirming the underground state of the piles, which cannot be visually seen during normal press-in of piles.
Besides allowing the management and confirmation of far-away sites such those overseas, it also allows a single operator to operate and support several machines operating in a remote location. It can be expected to alleviate the shortage of engineers and improve labour productivity.
* A technology that reproduces a real-world environment in virtual space by using information obtained from the real world
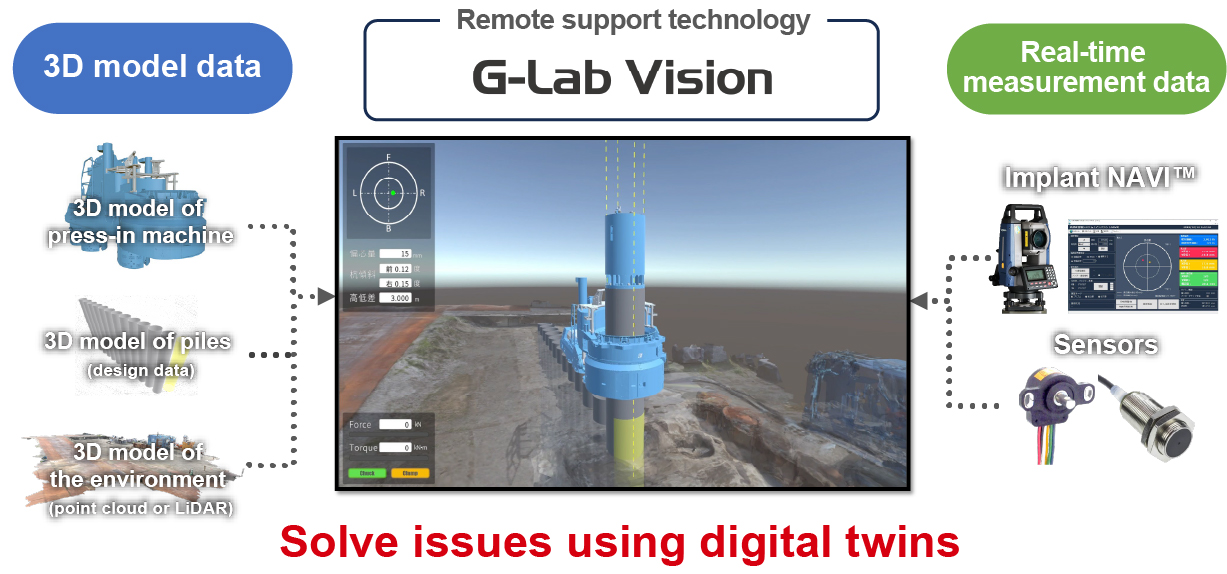
➤ Scope of Verification and Results (2): Process feasibility under remote support
Using a digital twin, an operator at a place away from the site was able to collaborate with site workers to complete processes from the pitching of piles to the alignment of pile heads*. Going forwards, improvements will be made based on feedback from users to further enhance usability.
* Levelling of the upper positions of the pressed-in piles
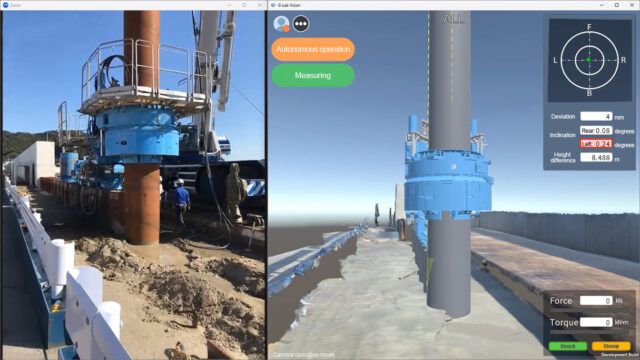
Operation screen of G-Lab Vision
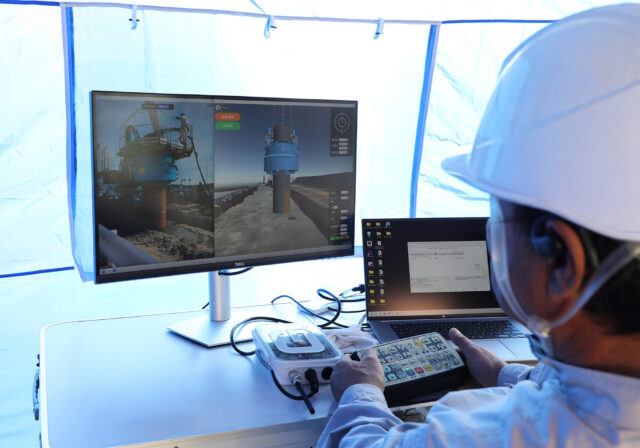
During operation of G-Lab Vision
■Profile of GIKEN Group
GIKEN developed SILENT PILERTM, the world’s first reaction-based hydraulic pile jacking machine, installing piles without noise or vibration. GIKEN Group now actively promotes its press-in technology worldwide and contributes to the construction industry by proposing and implementing innovative solutions. The innovative press-in technology provides a unique solution and the adoption of this technology has spread to over 40 nations and regions.
Contact Us