Originally founded as a "pollution control company," we have provided solutions to environmental problems through our business, contributing to the formation of a sustainable society. Furthermore, we have started a carbon neutrality project in order to advance our efforts to achieve carbon neutrality by FY2050. Through this project, we have calculated CO2 emissions associated with the Group's activities, set reduction targets and implemented actions towards reduction.
GIKEN Group Supply Chain Emissions for Year Ending in August 2023
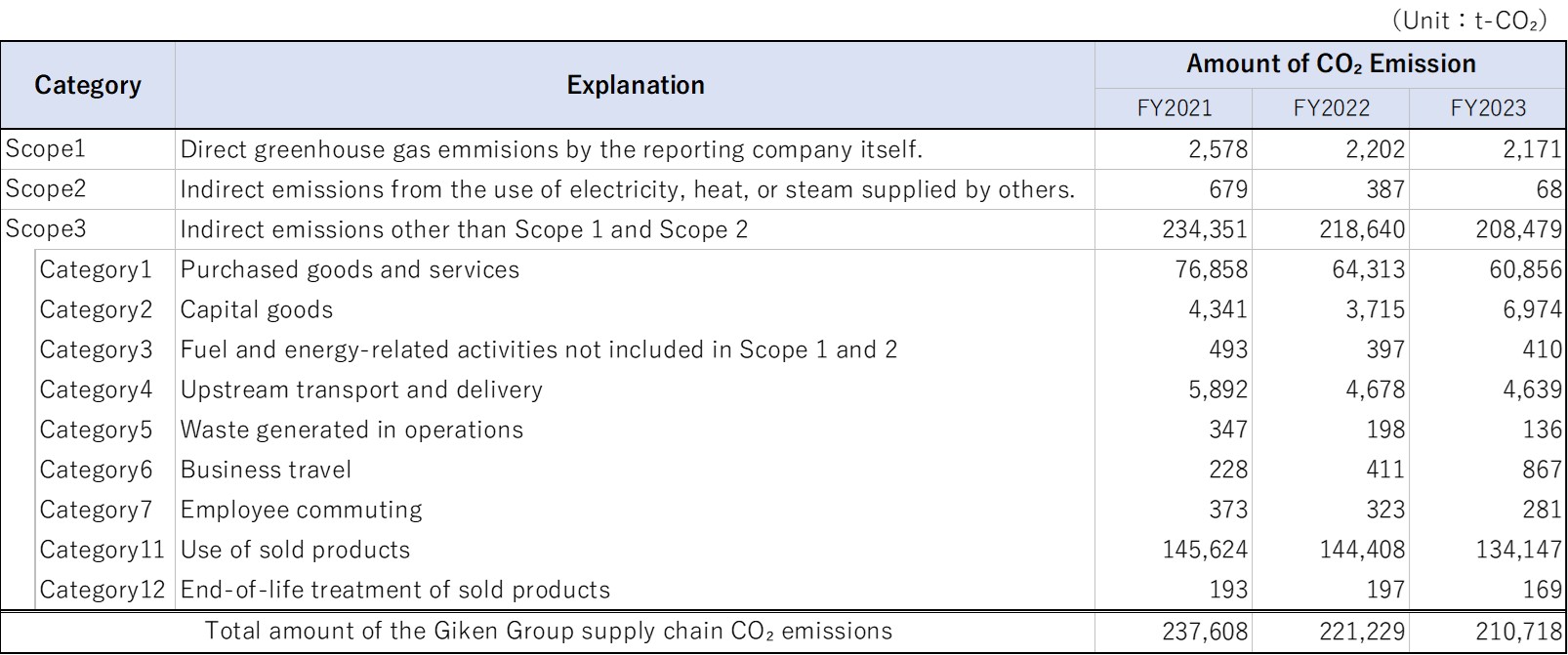
*Calculated based on GHG Protocol guidelines for GIKEN LTD. and its consolidated subsidiaries.
*Scope 2 is calculated based on market standards.
*Within Scope 3, the following categories are excluded from the calculation because they do not apply to our business.
Category 9 (Downstream Transportation and Distribution), 10 (Processing of Sold Products), 14 (Franchises), 15 (investments)
*Within Scope 3, Category 8 (Upstream Leased Assets) is included in Scope 1 and 2 for calculations.
*Within Scope 3, Category 13 (Downstream Leased Assets) is included in Category 11 for calculation.
*Totals may not add up due to rounding.
GIKEN Group Supply Chain Emissions Reduction Target for Year Ending in August 2031
Classification | Target Year | Target |
Scope 1, 2 | Year ending August 31, 2031 | 42% reduction from year ended August 31, 2021 |
Scope 3 | Year ending August 31, 2031 | 25% reduction from year ended August 31, 2021 |
Reduction Actions by the GIKEN Group (Accomplishments)
Switch to Renewable Energy
From May 1, 2022, the power used in all company offices and factories (7 locations in Japan) have been switched to virtually 100% renewable energy.

Introduction of Modal Shift
From 2022, transportation of certain products and parts has been moved to rail or ferry from truck.
Compared to truck transportation, an over 5% per year reduction of CO2 emissions has been found in trial calculations.
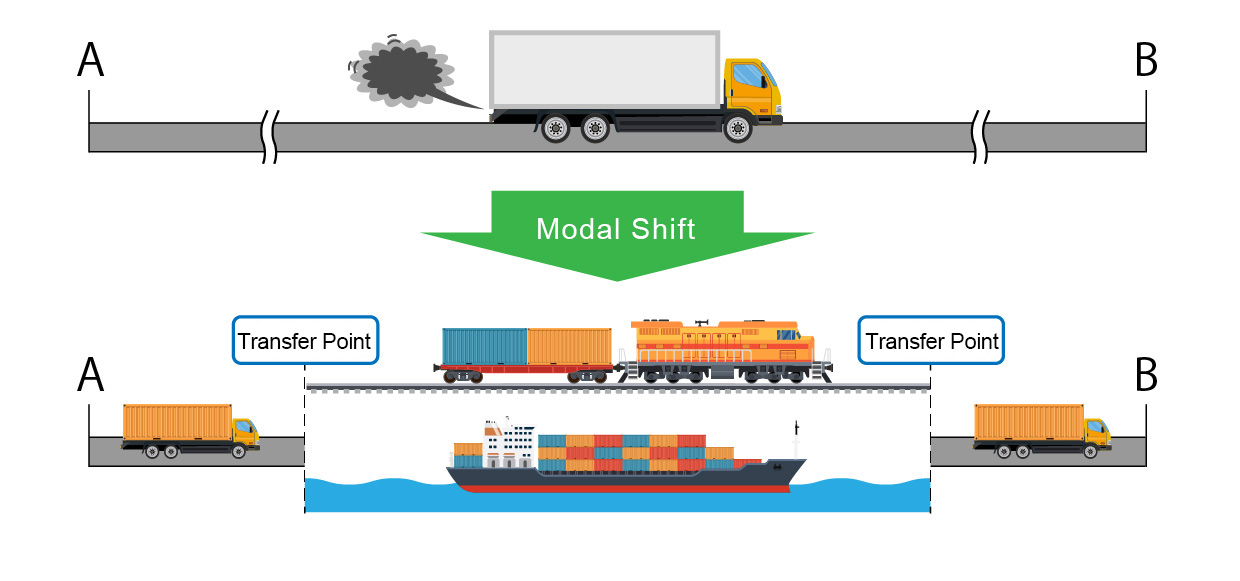
Re-Evaluation of Packing Materials
Certain cardboard packaging has been switched to containers to reduce waste.
Additionally, we have re-evaluated our use of air bubble packaging. Unnecessary packaging has been eliminated, and low CO2 emission air bubble packaging is being utilised when the use of air bubble packaging is necessary.
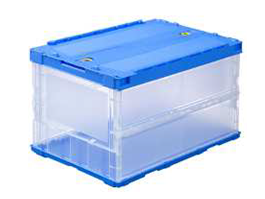
Re-Evaluation of Packing Materials
・Certain cardboard packaging
has been switched to containers.
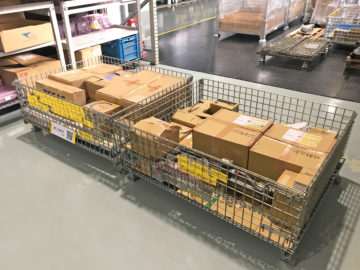
Before
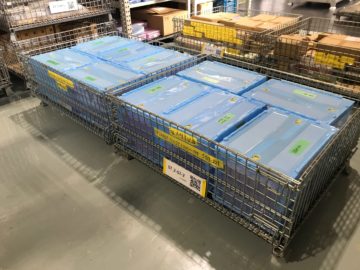
After
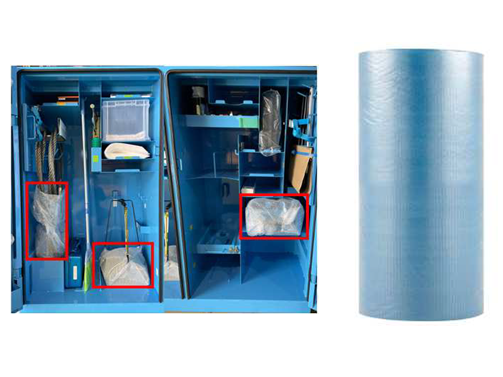
Re-Evaluation of Packing Materials
・Elimination of unnecessary packaging
・Use of low CO2 emission air bubble packaging
Regarding the use of biofuels
We are promoting the use of biofuels as an alternative to diesel fuel, enhancing the environmental performance of our products, and striving to reduce CO₂ emissions throughout our supply chain.
Contribution to the Environment Through Superior Construction Methods
Our products and methods, such as SILENT PILER™, have been designed and developed based on the Press-in Principle, and we also offer GRB SystemTM equipment that can complete the work while advancing along the top of already installed piles. Using these machinery and methods, temporary construction work can be minimised, avoiding the need for temporary platforms that other pile-driving machines might require. This approach shortens the construction period and reduces the use of construction materials, leading to a reduction in CO2 emissions.
*For more information see : GRB SystemTM, Superiority of the press-in principle.
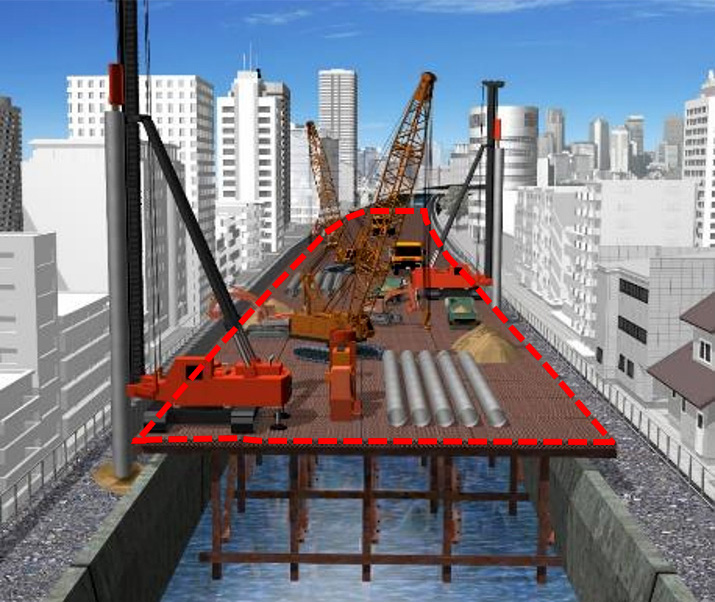
Other Methods
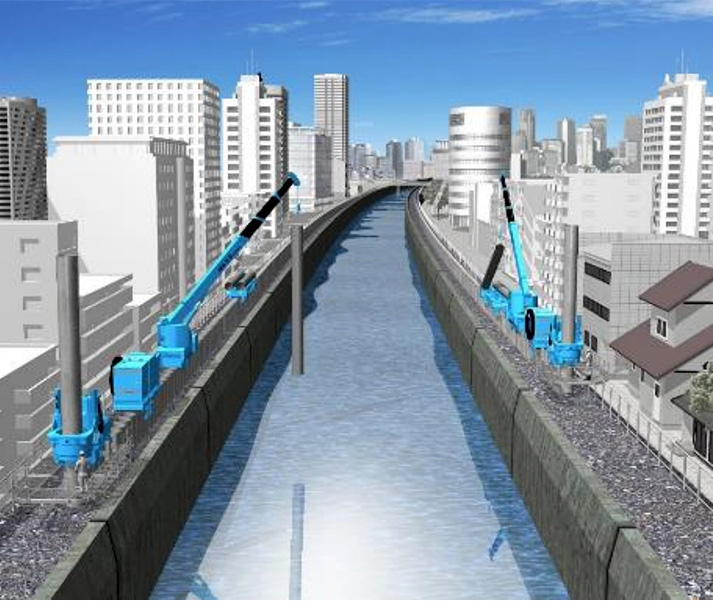
GIKEN Method
No need for temporary works that are required with other construction methods (manufacturing, transporting, installing and removing temporary materials)
⇓
Reduction in CO2 emissions
Shortened construction period
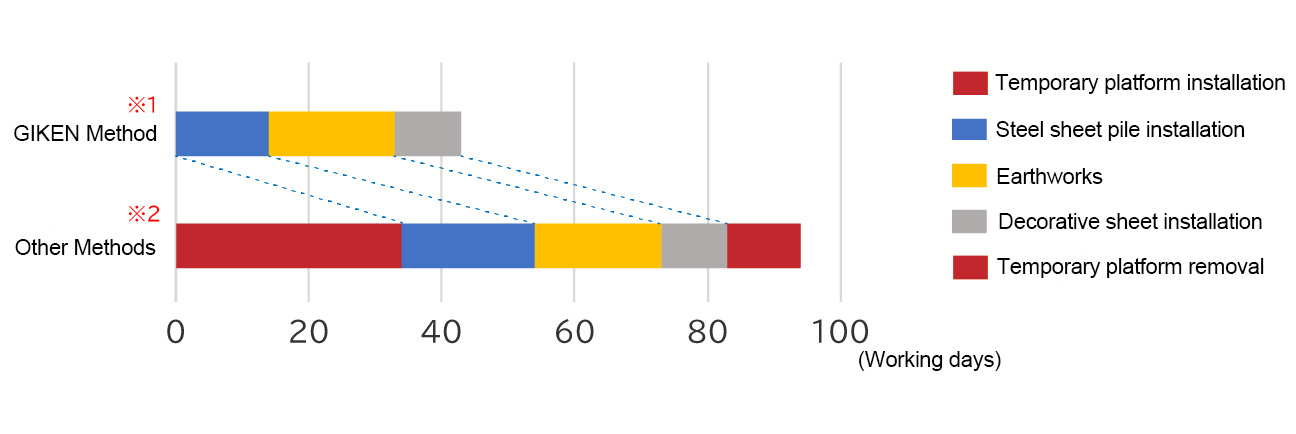
*1 Standard technical data on tubular sheet pipe press-in construction, Tubular Sheet Pile Press-in Method, Japan Press-in Association (2022 version)
*2 Standard estimation standard for civil engineering, Japanese Ministry of Land, Infrastructure, Transport and Tourism (2022 version)
Reduced construction materials
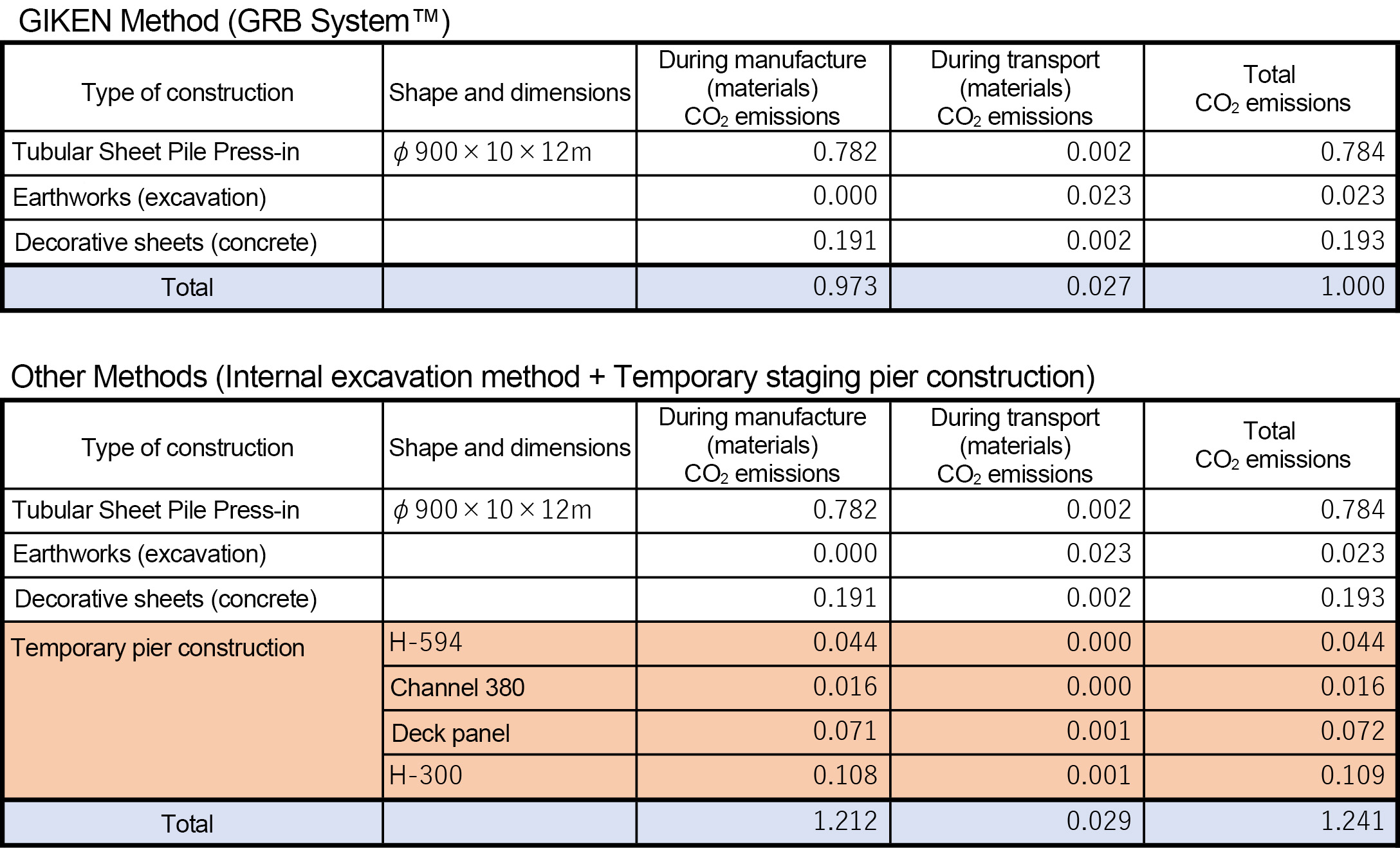
*Prepared by GIKEN LTD. based on Design and Construction Guideline for Press-in Piling 2020, International Press-in Association