The Implant Structure consists of robust and durable structural members which are firmly embedded into the ground by the Press-in Method. The structural members are selected from a wide variety of piling materials in accordance with design requirement, thus, the Implant Structure can cover a wide range of foundation designs required in today’s construction industry. Also, being embedded into the ground, the Implant Structure is extremely resilient and maintains its serviceability even in extreme events, such as natural disasters.
Deep-rooted Resilient Structures
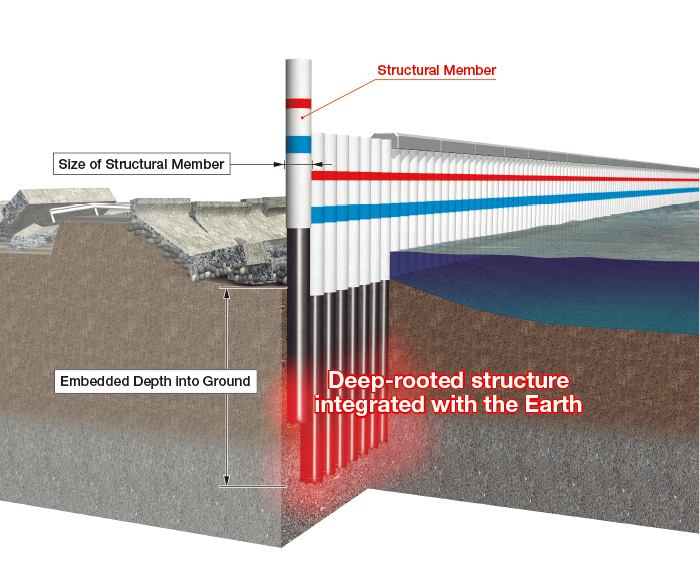
Rapid Construction with Minimal Footprint
Traditional gravity structures are commonly used worldwide as they are simply constructed by "seating" on firm ground. However, they are quite vulnerable to dynamic loads caused by floods, wave actions, earthquakes and tsunamis. Furthermore, gravity foundations require a large footprint. This leads to complex construction processes i.e. temporary retaining walls, bulk excavation, shoring and backfilling etc. On the other hand, the Implant Structure is directly installed into the ground forming an extremely resilient structure with a minimal footprint and construction process.
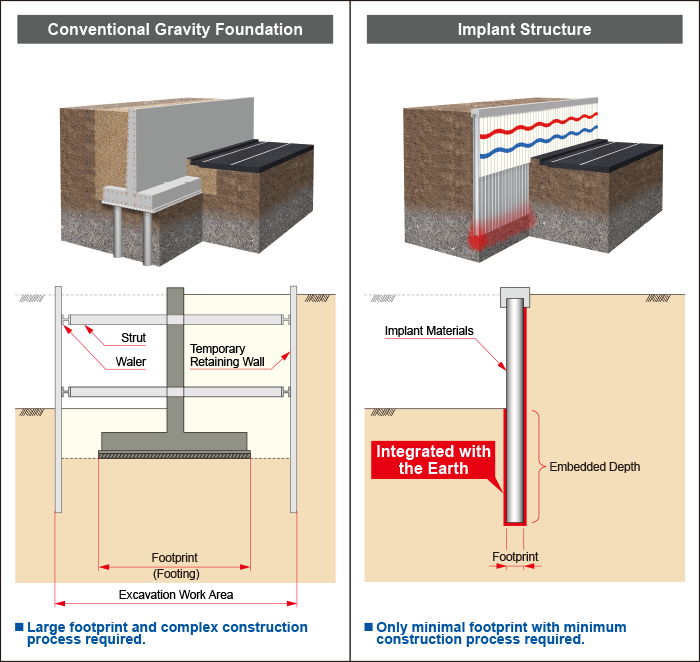
Traditional "Gravity Structures" can be constructed by using general construction materials i.e. soil and concrete, and simple techniques i.e. soil excavation and backfilling. However, gravity structures require a large footprint and complex construction sequences. This lead to a difficulty in removing or upgrading the structure and therefore, gravity structures are normally constructed based on the "Scrap & Build Concept ". On the other hand, with the "Implant Structure", high yield materials are directly embedded into the ground with a minimal footprint and construction sequence. Thus, the Implant Structure can easily be removed, deepened and strengthened during its design life, based on the "Reusable and Upgradable Design Concept".
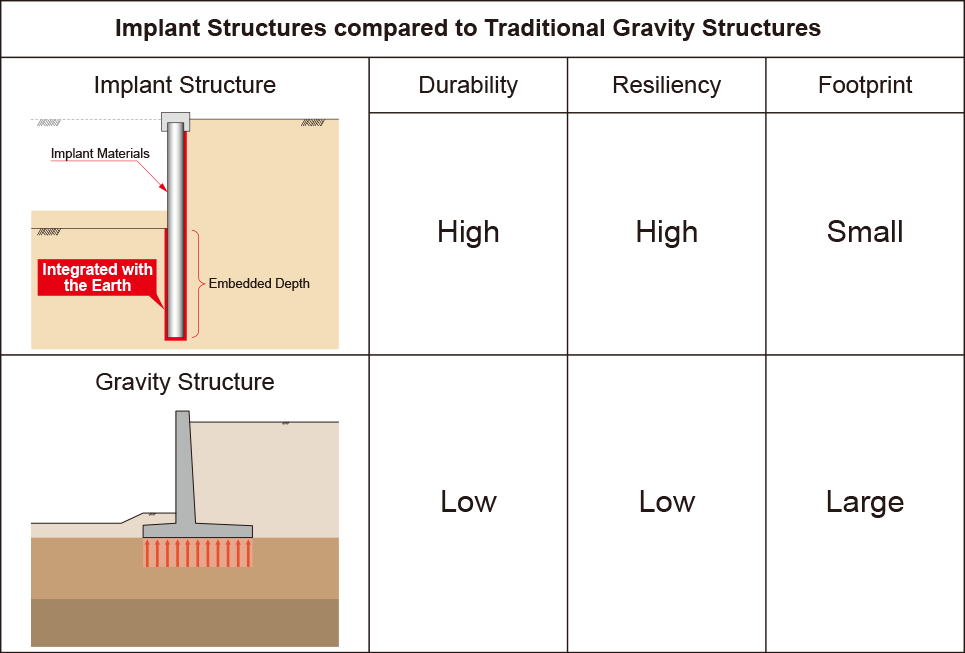
The difference in structural strength is obvious!
This animation simply shows the difference between Implant Structure and gravity structures.
Implant Structure vs Gravity Structures (Reduced Scale Model Tsunami Testing)
This video compares the resilience of Implant Structure to gravity structures against tsunamis. The models for the test are an Implant Structure (tubular pile wall) and a gravity structure (concrete caissons) on a scale of 1/33. This apparatus can simulate the maximum wave-height of 6m and wave velocity between 10-15m per second.
Comparison of Implant Structure and Traditional Gravity Structures
Structural Damage caused by earthquakes and Tsunamis
In March 2011, the Great East Japan Earthquake struck the north east region of Japan with a magnitude of 9 on Richter scale and seismic intensity of 7. Because the massive earthquakes were submarine earthquakes, tsunamis struck the coastlines shortly after the events with a maximum wave height of 16.7m.
Due to the devastating dynamic loads from the earthquakes and tsunamis, a majority of traditional gravity structures on the coastlines were instantly destroyed without adequate resistance. However, it was reported that some embedded structures well withstood the tremors and tsunamis, remaining in place. It was a clear comparison of gravity structures and embedded structures in terms of structural resiliency. As a seawall or levee, the most important aspect is not stiffness of the structure itself, but resiliency, which can absorb, dissipate or mitigate the impact of disasters.
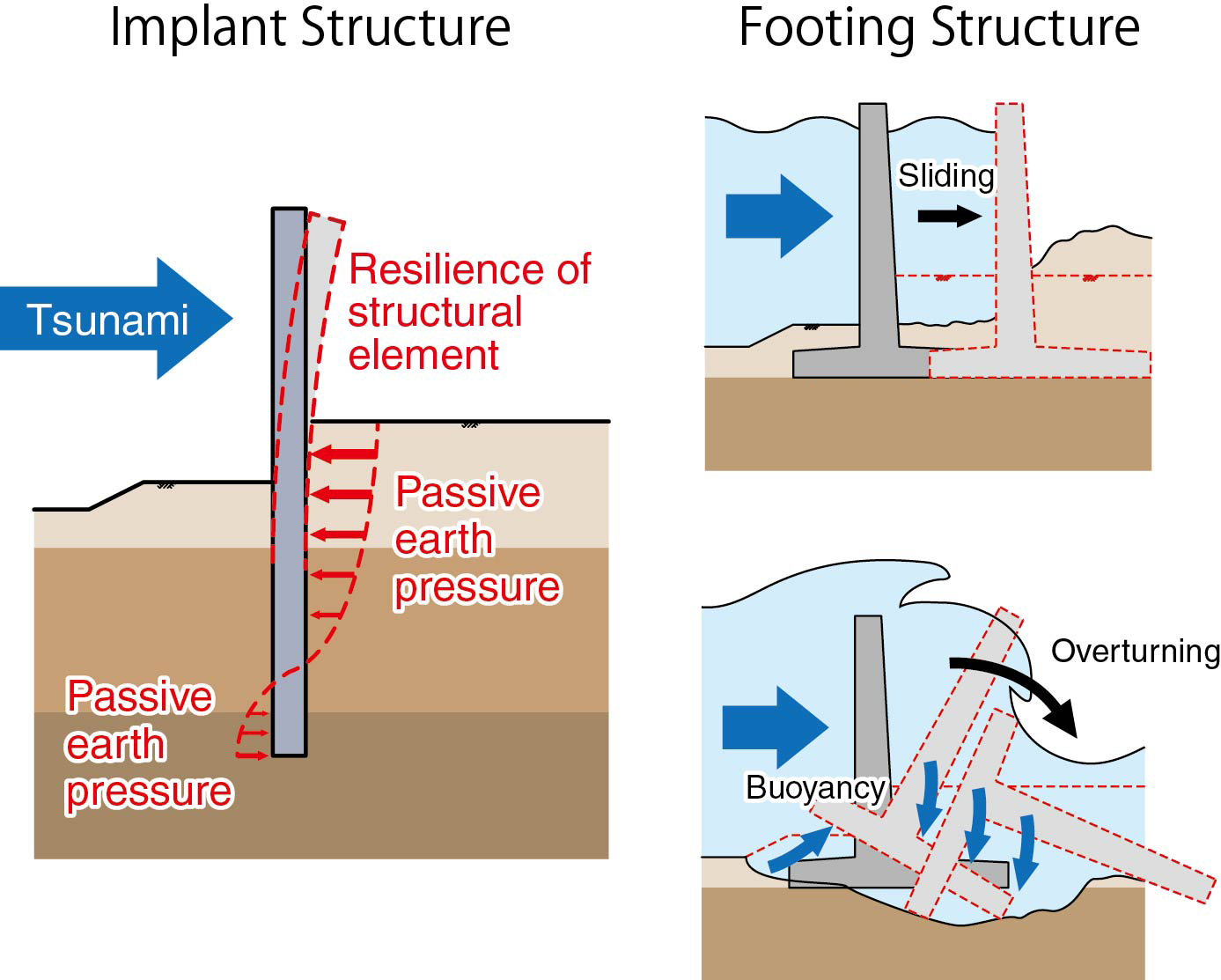
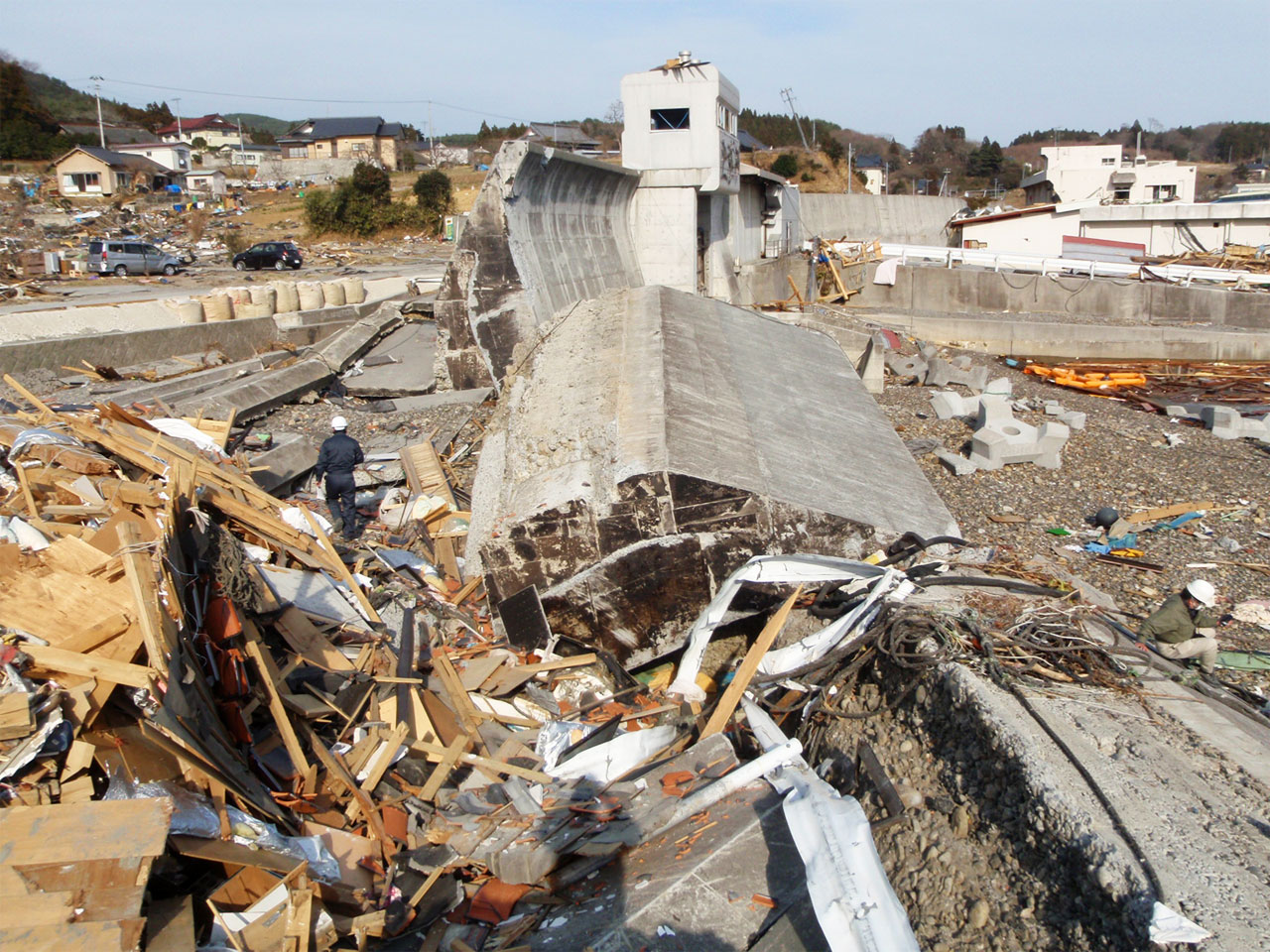
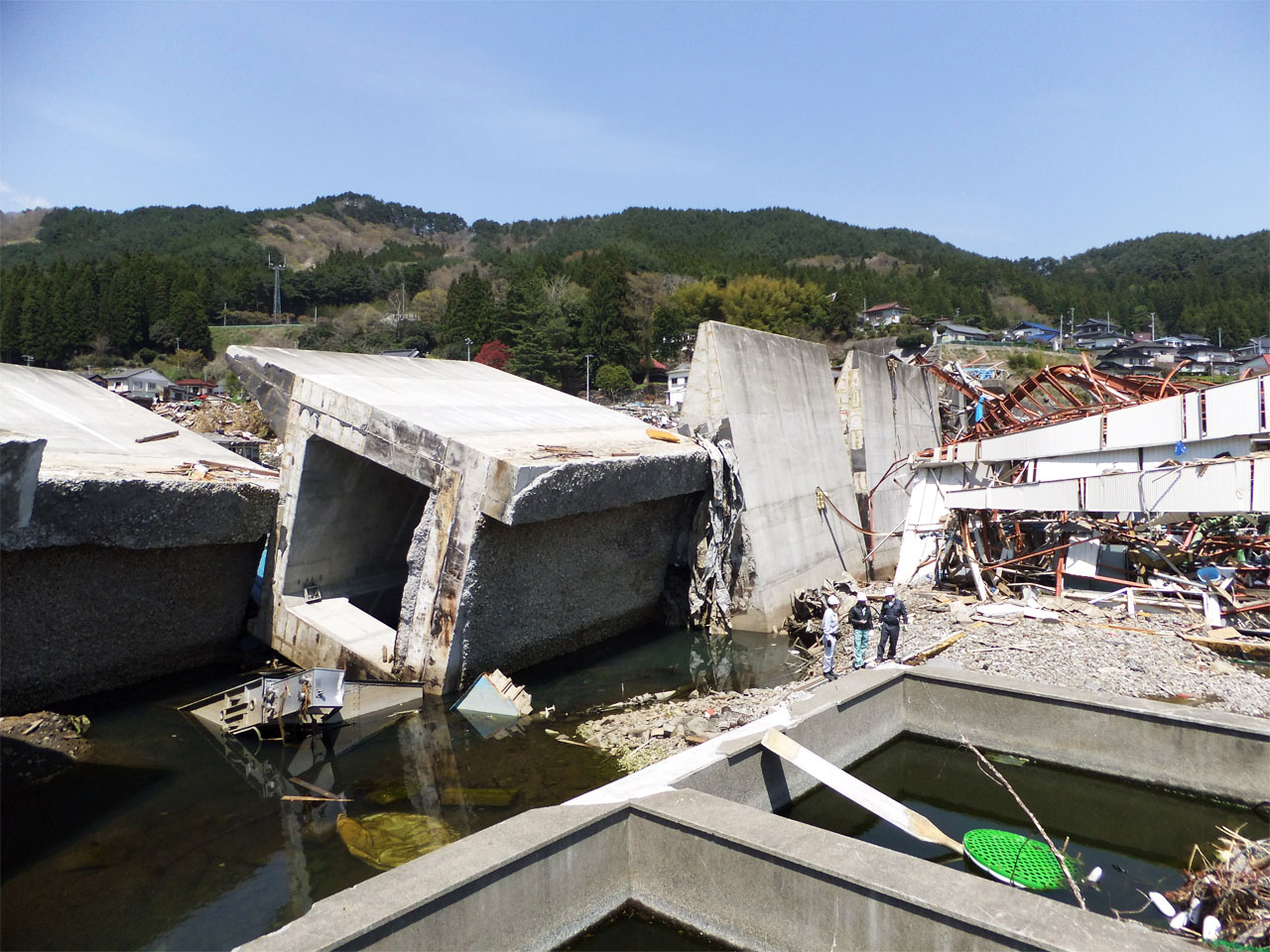
Destroyed RC Seawall (left) and Caisson Type Seawall (right)
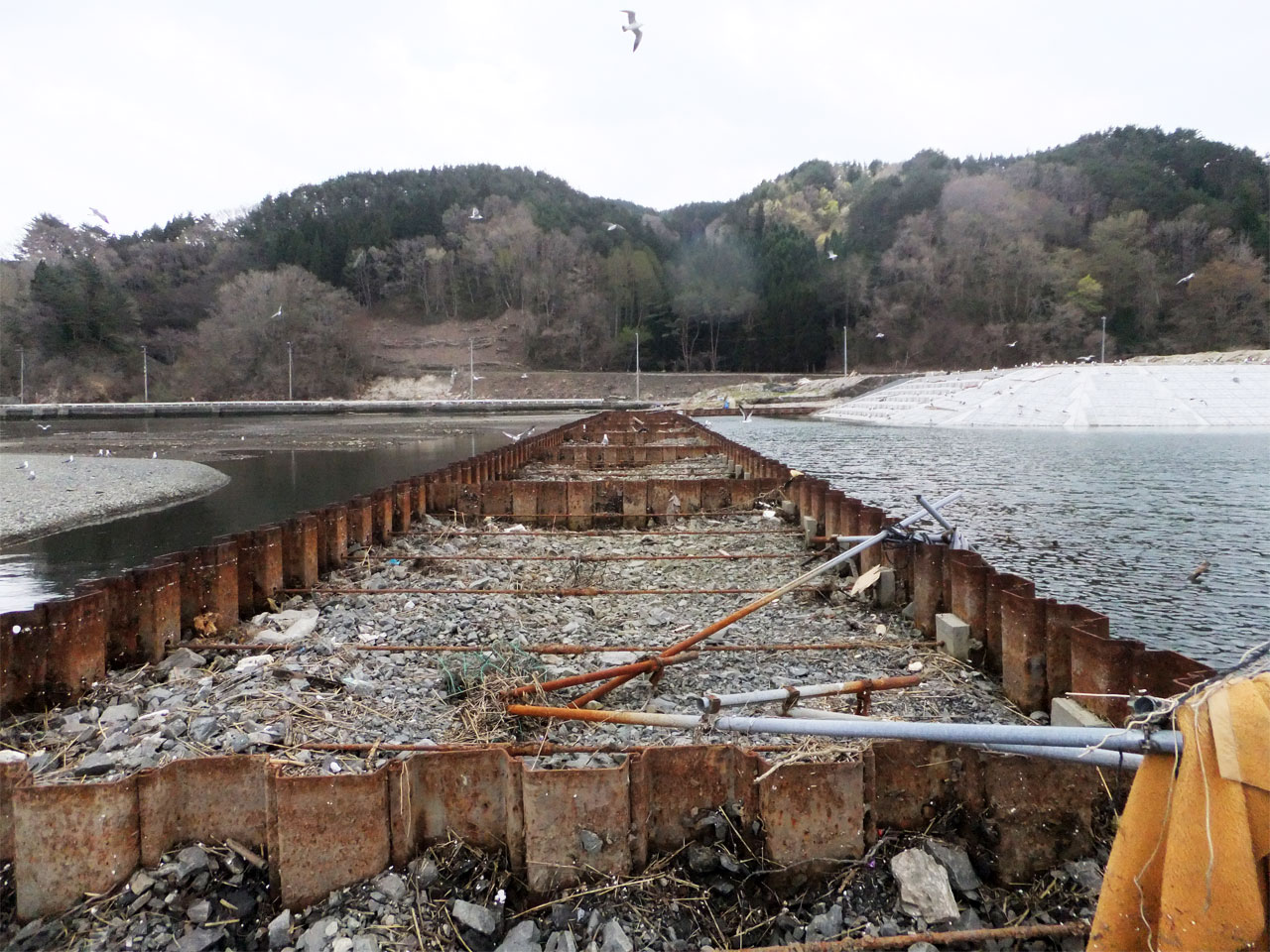
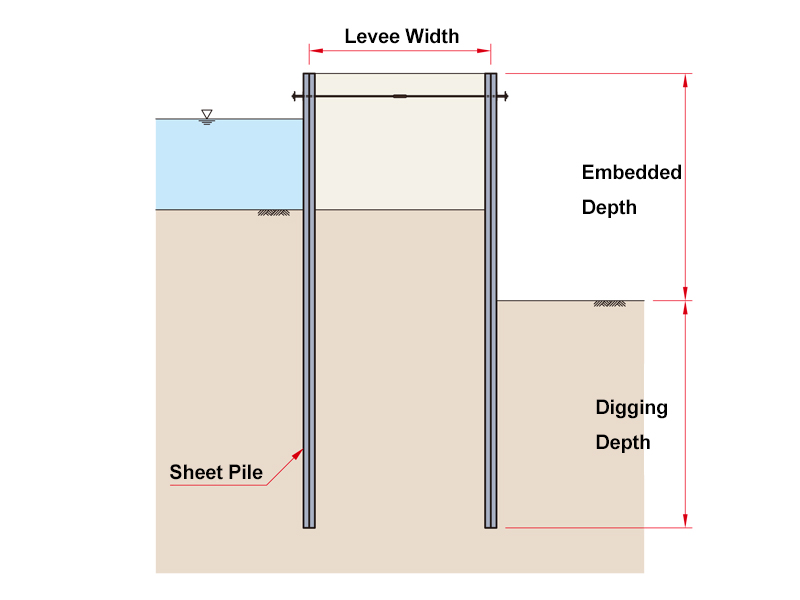
Intact Embedded Structure (Twin Sheet Pile Wall Cofferdam)
PPT ( Pile Penetration Testing ) Thorough pile monitoring method ensures a total observational construction process.
With the Press-in Monitoring System, real-time data logging of the Press-in operation is available during each pile installation. These are Press-in Force, Extraction Force, Auger Torque, Chuck Rotation Torque, Elapsed Time etc. Then, this monitoring data can be correlated with the D.V.L. (Design Verification Load). Based on the correlation, it is ensured that the bearing capacity of each pile exceeds the D.V.L. This thorough pile monitoring approach is called PPT (Pile Penetration Testing), which guarantees a total observational construction process.
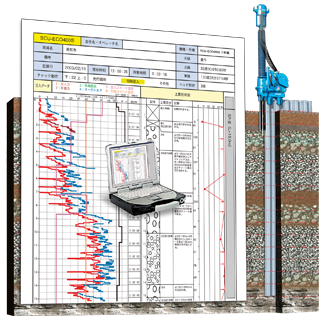