GIKEN LTD. (Head Office: Kochi, Japan President: Shinnosuke Moribe) has developed an electrified Gyro PilerTM "GRV0611e" and GRBTM system that enables zero exhaust gas emission during pile installation works.
In anticipation of decarbonization, the new press-in machine is fully electrified and will be the next-generation Press-in system of GIKEN. It will not exhaust gas, and its construction efficiency is dramatically improved compared with our existing Press-in machine.
The newly developed model was shipped on December 3, 2021, for the World Heritage listed Canal Project* in the Netherlands, and the project's pilot phase is scheduled to begin in 2022. We will showcase the next-generation press-in machine at a project attracting global attention in the Netherlands, where environmental regulations are advanced. We expect this to be an excellent opportunity to highlight the newly developed Press-in System, which contributes to SDGs.
GIKEN will continue developing the GRV0611e lighter, compact, and efficient and will apply the techniques to other mass-produced models.
"No vibration and no noise," "Space-saving construction," and "Temporary work platform free construction"-. In addition to these advantages of the Press-in principle, we will make "Zero CO2 Emissions during pile installation" the new strength and accelerate the expansion of the Press-in system and The Implant™ Method globally.
※ A quay wall renovation project for Amsterdam's World Heritage-listed canal District. GIKEN was awarded first place in the international call for Innovation Partners of the City of Amsterdam with its G-Kracht partners. For details of the project, please view the previous news release (https://www.giken.com/en/release/22_may_2020/)(https://www.giken.com/en/release/5_jul_2021/) .

■Major Features of GRV0611e
[Driven by an electric motor]
The current Press-in machines use fossil fuels to turn the engine and drive hydraulic pumps. The GRV0611e obtains the machine's hydraulic power by moving the hydraulic pump with an electric motor. When electricity is drawn from the grid, gas emissions at construction sites, including electricity procurement, can be zero.
With the view to achieving zero emission in construction sites worldwide, we are in the progress of developing a Press-in system that will operate with batteries.
[Dramatically increases construction efficiency]
The piling installation efficiency has dramatically improved by electrifying the Chuck Rotation motor, where the "pile to be pressed-in" are grasped. The Gyro Piler, installs piles by rotation with the assistance of cutting ring bits attached to the pile toe. This enables the installation of tubular piles through existing reinforced concrete structures and hard ground.
The rotation rate of the existing hydraulic Gyro Piler (applicable to 500mm and 600mm tubular pile) was up to 6.8 times per minute, while the electrified GRV0611e has increased by more than three times, up to 23 times. Furthermore, the rotation speed lowers as the rotation torque increases on conventional machines, but the electrified type can maintain the rotation speed.
[Lighter and compact, contributes to cost reduction]
Compared with the engine-type Power Unit, the number of machine parts of the electric Power Unit is one-third. This makes the machine lighter and more compact. Fewer machine parts will also reduce environmental load such as CO2 generated during the manufacture, maintenance and disposal of machine parts, as well as the costs.
■Features of the electrified GRB™ System
As shown on below figure, the component of the GRB™ system is the Press-in machine main body, "Clamp Crane" which pitches piles, "Power Unit" which is a hydraulic power source, and "Unit Runner" which moves the Power Unit, and "Pile Runner” which transports piles. The electrified system will supply power to the Power Unit via a power grid or generators.
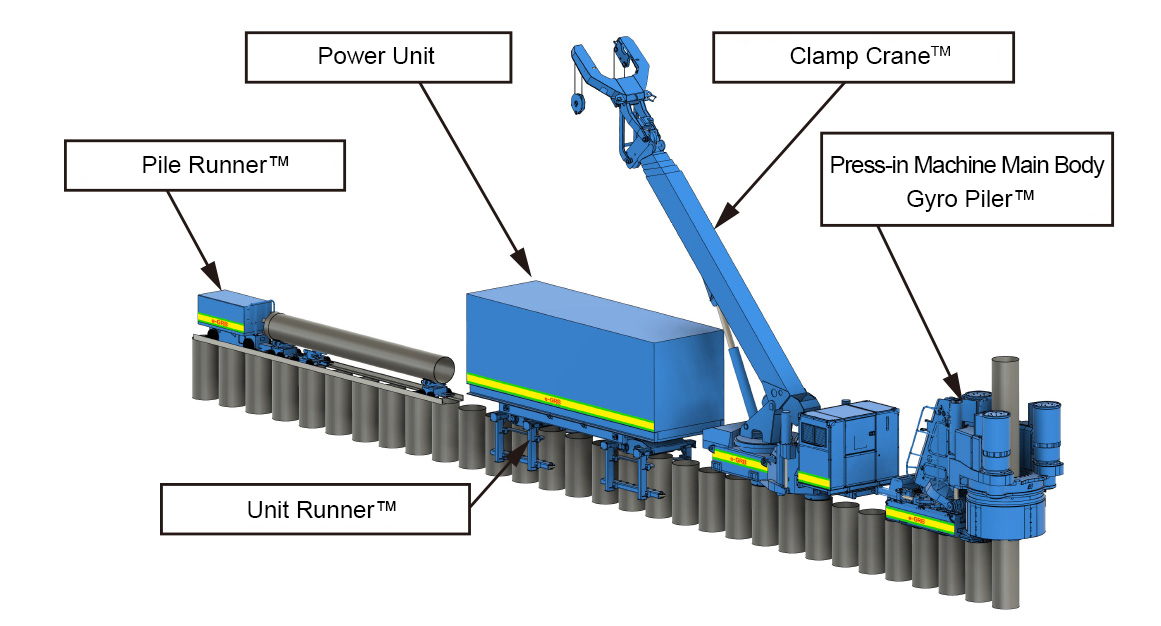
■Future Outlook
We have contributed to reducing the CO2 in piling installation using the GRB™ system, which eliminates the need for a working platform. The development of the electrified Press-in system has made it possible to further contribute to decarbonization.
Once the electrified Press-in System is widely used and replaces the engine-powered models, it will eliminate the cost to develop compatible models whenever emission regulations progress. We will continue to work quickly on developing and disseminating Press-in machines that reduce environmental impact and contribute to realizing a decarbonized society.
■Specification of GRV0611e
Applicable Piles | Tubular pile φ500, φ600 mm |
Maximum Press-in Force | 1100 kN |
Maximum Extraction Force | 1200 kN |
Maximum Chuck Rotation Torque | 320 kN・m |
Maximum Chuck Rotation Velocity | 23.0 min-1 |
Chuck Up/Down Stroke length | 1200 mm |
Rotating Press-in speed | 0.5~6.4 m/min |
Rotating Extraction speed | 0.5~4.8 m/min |
Machine Weight | 20500 kg (φ500mm) |
■Profile of GIKEN Group
GIKEN developed the SILENT PILER, the world's first reaction-based hydraulic pile jacking machine, installing piles with no noise and vibration. GIKEN Group now actively promotes the Press-in Technology worldwide and contributes to the construction industry by proposing and implementing innovative solutions. The innovative technology of press-in provides a unique solution and the adoption of this technology has grown to more than 40 nations and regions.
GIKEN LTD.
International Business Department
TEL: +81-3-3528-1633 (weekdays: 8:30 to 17:30)
Tokyo Head Office: 16F Ariake Central Tower, 3-7-18 Ariake, Koto-ku, 135-0063, Japan