GIKEN LTD. sends prayers and best wishes to everyone affected by the 2024 Noto Peninsula Earthquake followed by the heavy rainfall in Noto Peninsula in September 2024.
The GYRO PILER™ rotary cutting press-in machine for tubular piles of GIKEN LTD. (Head Office: Kochi-shi, Kochi; President and CEO: Atsushi Ohira; hereafter “GIKEN”) was employed in reinforcement work for the cleared road leading to Noto Ohashi bridge. The construction work was completed by GIKEN SEKO CO., LTD. (Head Office: Kochi-shi, Kochi; President and CEO: Akihiro Nishigawa; hereafter “GIKEN SEKO”), a company of the GIKEN Group, while preventing landslide on the side of the bridge’ abutment. The vicinity of Noto Ohashi bridge suffered severe damage—such as road collapse—due to the 2024 Noto Peninsula Earthquake, and for some time, only the Noto-Satoyama Kaido expressway continued to be restricted to alternate two-way traffic using a single lane. Through this road reinforcement work, two-way traffic across all sections of the expressway became possible on September 10.
At the construction site, out of the two lanes used for both directions, there was the risk that the slope on the side of the abutment would collapse again for the lane toward Kanazawa, making the building of a retaining wall an urgent issue. It was also necessary to keep the lane leading away from Kanazawa—which was being used for alternate two-way traffic—open during construction. As such, the GRB System™, which does not require a temporary platform for working space unlike other construction methods, was employed. Small and lightweight machinery grabbed firmly onto driven piles and operated on top of the pile to complete the work. The construction was completed safely and promptly within a narrow space that was prone to collapse.
Comments from the Ministry —the project owner—and road users include being surprised that the series of work from the mobilisation of press-in machines to their assembly and the conduct of press-in work could be undertaken within that narrow space, showing a high level of interest in the technologies of GIKEN. At the disaster-affected areas, there are still many places left severely damaged by the earthquake as well as the Noto Peninsula heavy rainfall in September 2024. Centered on the Noto Reconstruction Support Office, a temporary office in Kanazawa-shi, Ishikawa Prefecture, the GIKEN Group will continue to gather and provide information to further accelerate the restoration of the disaster-affected areas.
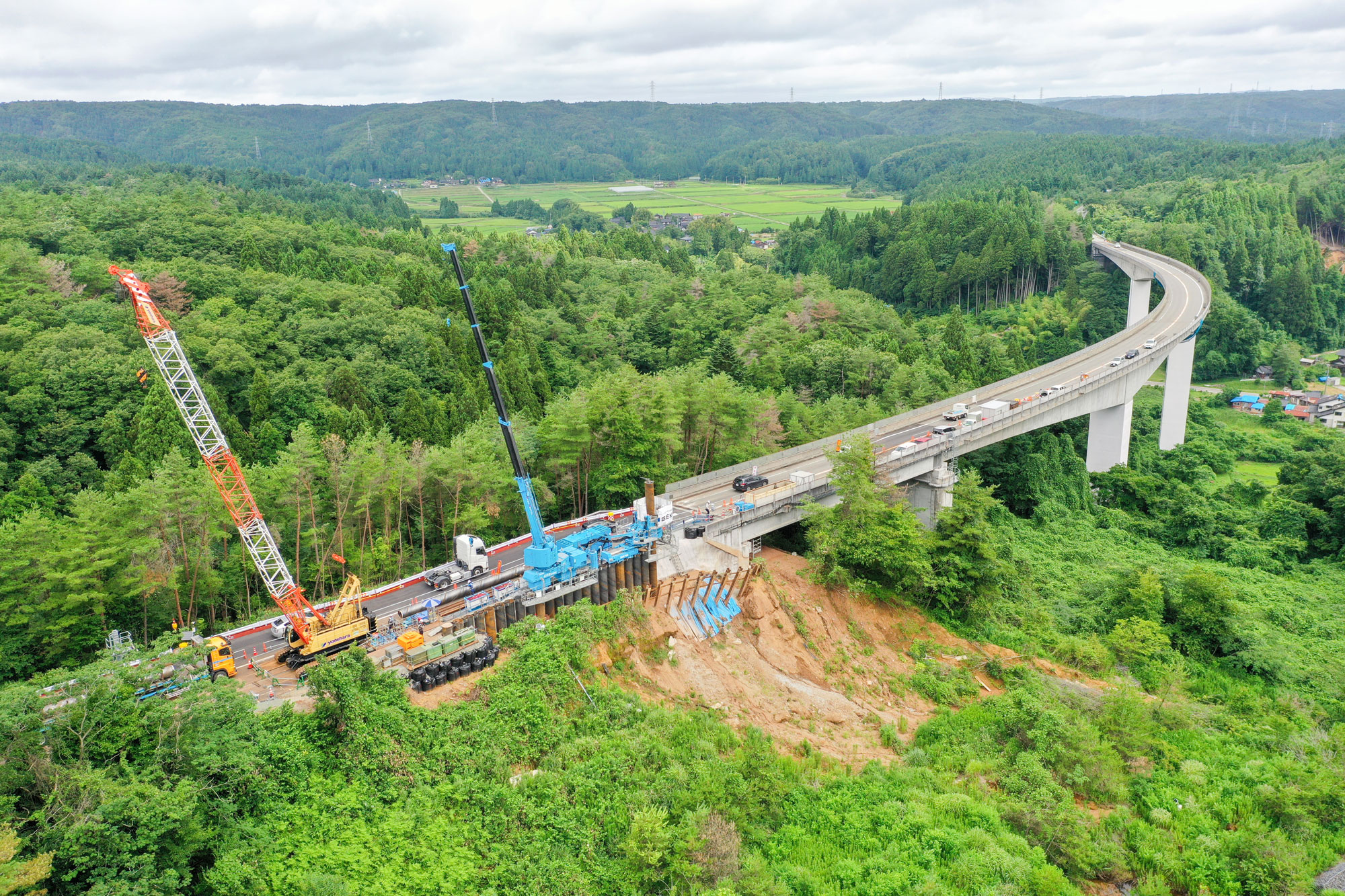
■Construction Details
The site was a section of the Noto-Satoyama Kaido expressway, a major artery in the Noto region that had supported its economy, near the abutment that forms the start of Noto Ohashi bridge. A portion of the two-lane, two-way road collapsed due to the 2024 Noto Peninsula Earthquake. The slope on the abutment side became prone to collapse, and the road continued to be restricted to alternate two-way traffic using a single lane due to fear that the lane toward Kanazawa would collapse again while being used.
The GYRO PILER™ F401-G1200 and GRB System™ were employed for the work, which entailed pressing in 34 tubular piles measuring 23.5 m in length and 800 mm in diameter. A retaining wall extending 34 m was constructed.
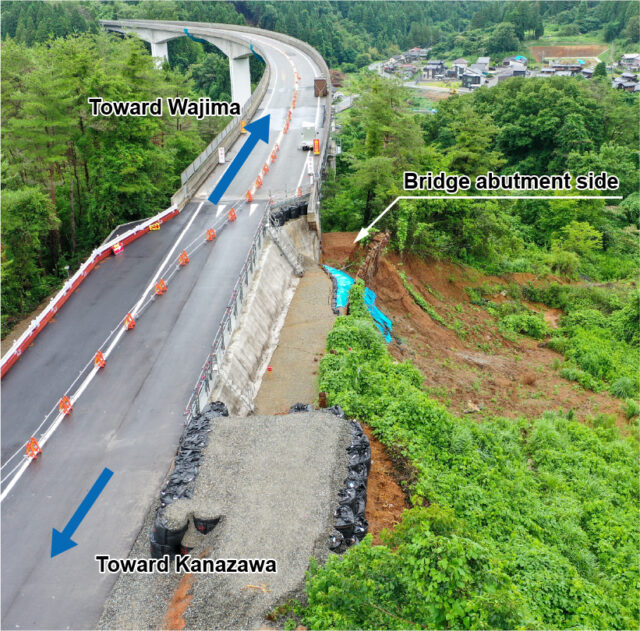
Before construction
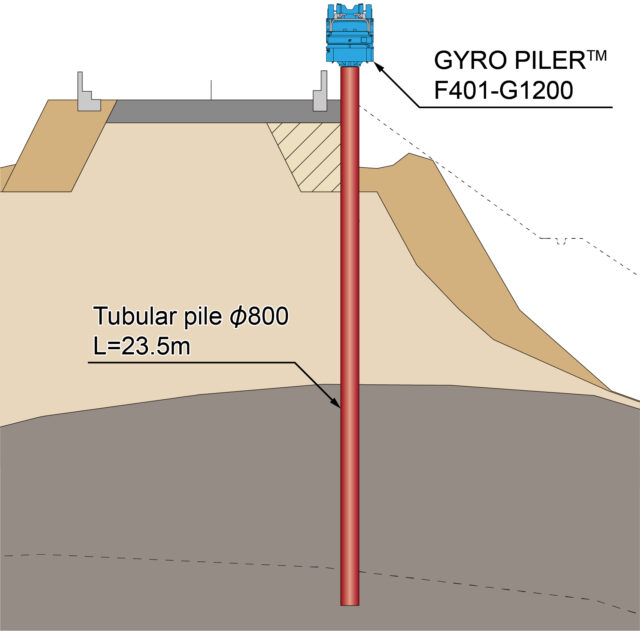
Construction cross-section
Produced by GIKEN LTD. based on data provided by Kajima Corporation
■Reason for Adoption
Issues with construction time and such when using other construction methods
Other construction methods require things like large heavy machinery, cranes, and materials to be placed on stable surfaces with no risk of falling over during construction. This would make it necessary to use the lane leading away from Kanazawa in this case because of lack of space, which would inevitably result in road blockages. To maintain traffic flow, it would be necessary to construct temporary platforms on the slope as working space, but the slope was prone to collapse and the temporary work would incur time and cost. Construction methods that employ large vibration pile drivers would have created additional concerns about potential further collapses because the vibration affects the ground itself. Furthermore, there was a high possibility that it would be necessary to remove buried boulders during construction, which would have extended the time needed for construction.
Fast completion without temporary work, vibration, or noise
The GRB System™ is a system that works from on top of the piles when carrying out the press-in construction work, from pitching to pressing in new piles. There is no risk of falling over in principle as the machinery is small and lightweight and it firmly grips the driven piles. In addition, the GYRO PILER™ allows construction to proceed with minimal vibration. As tubular piles with cutting claws installed on the tip are pressed in using rotation, it can rapidly construct tough structures while penetrating hard ground such as boulders as well as existing structures. The superiority of GIKEN—such as construction without temporary work, vibration, or noise—was applied this time to achieve construction with high safety, speed, and economy.
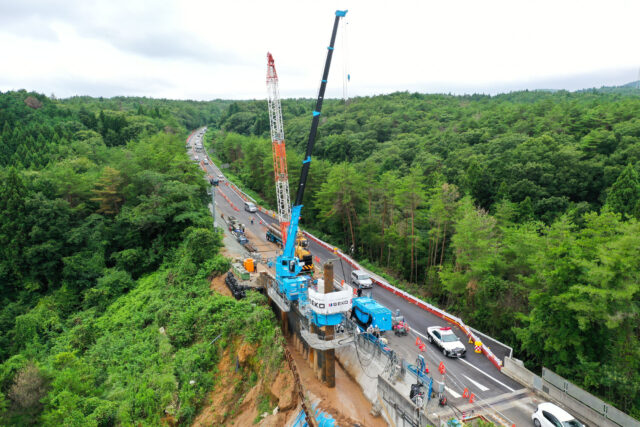
Construction while maintaining alternate two-way traffic using a single lane
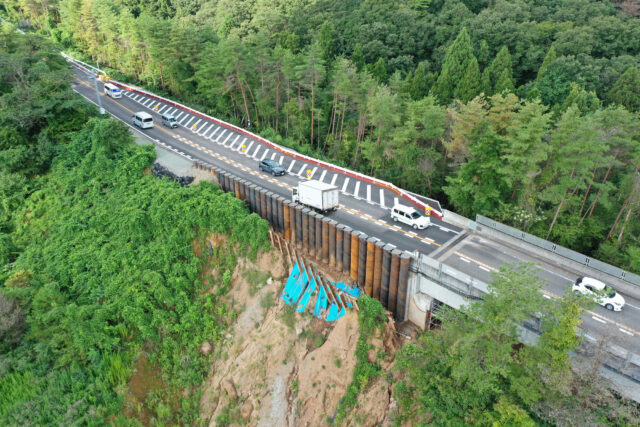
Two-way traffic possible since September 10 upon completion of the press-in work
■ Project Summary
Project Name | 2024 Noto Peninsula Earthquake Nouetsu Expressway Road Clearing Project Phase 6 |
---|---|
Location | Section from Uwano, Anamizu-machi, Hosu-gun, Ishikawa Prefecture to Koshinohara, Anamizu-machi, Hosu-gun, Ishikawa Prefecture |
Project Owner | Hokuriku Regional Development Bureau , Ministry of Land, Infrastructure, Transport and Tourism |
Main contractor | Kajima Corporation |
Sub-contractor | GIKEN SEKO CO., LTD. |
Equipment | GYRO PILER™ F401-G1200 and CLAMP CRANE™ CB3-6 |
Specification of Pile Elements | 34 tubular piles (800 mm diameter, 23.5 m long, joined at one location) |
Press-in Construction Period | July 16 to August 5 2024 |
■Profile of GIKEN Group
GIKEN developed the SILENT PILER™, the world’s first reaction-based, non-vibratory hydraulic pile driving machine that operates with minimal noise impacts. The GIKEN Group now actively promotes its press-in technology worldwide and contributes to the construction industry by proposing and implementing innovative solutions. The innovative press-in technology provides a unique solution and the adoption of this technology has spread to over 40 nations and regions.
Contact Us