The all-at-once replacement work of bridge girders for the project to renew Daishi Expressway Bridge on the Shutoko, or Metropolitan Expressway, using pier foundations built with the ImplantTM Method of GIKEN LTD. (Head office: Kochi-shi, Kochi; President: Shinnosuke Moribe), was completed in June. Tubular sheet pile pier foundations*1, which offer considerable supportive strength, were chosen for the foundation work, and long piles, around 50 m in length, were pressed in. This ImplantTM Method was highly regarded for its high precision and safety in pressing in, and for allowing early completion. The press-in work was carried out by GIKEN SEKO CO., LTD., a Group company (Head office: Kochi-shi; President: Akihiro Nishigawa).
Building up a track record through projects, expectations for greater adoption in Shutoko Renewal Project.
Aging expressways is a national issue, and with the urgent need for major repairs and renewal work, amendments to the Road Development Special Measures Act and the act that allows tolls to be collected that were passed in May include a fifty-year extension of the period during which tolls will be collected, from its current 2065 to as late as 2115. These amended acts have allowed funding to be secured.*2 Work will continue in the future, including on measures for the aging expressways nationwide, and on making them four lanes.
A large-scale renewal project is being carried out on the Shutoko, which has supported the economy as a great artery of the Tokyo region. In this project, which is part of that work and has attracted the attention of people nationwide, we have already built up a substantial track record in foundation work, the basis of bridge repair, in the Haneda Line (Higashi-Shinagawa/Samezu) Renewal Project, and we can expect to see the ImplantTM Method adopted for any potential repair plans in the future. We shall continue to contribute to the sustained growth of the Japanese economy through building up our track record and offering engineering technologies to solve construction problems.
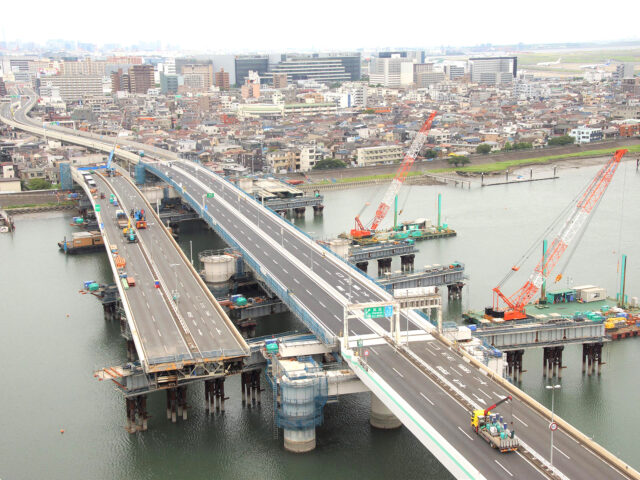
View of the all-at-once replacement work for the Daishi Expressway Bridge girders
Credit: Metropolitan Expressway Co., Ltd. / Photograph: KYOEI
*1. The foundation structure uses tubular sheet piles pressed in deep into the ground to enclose the soil, and then concrete is poured into this space.
*2. The Ministry of Land, Infrastructure, Transport and Tourism estimates that the total cost of expressway repairs needed by 2115 will top 8.3 trillion yen.
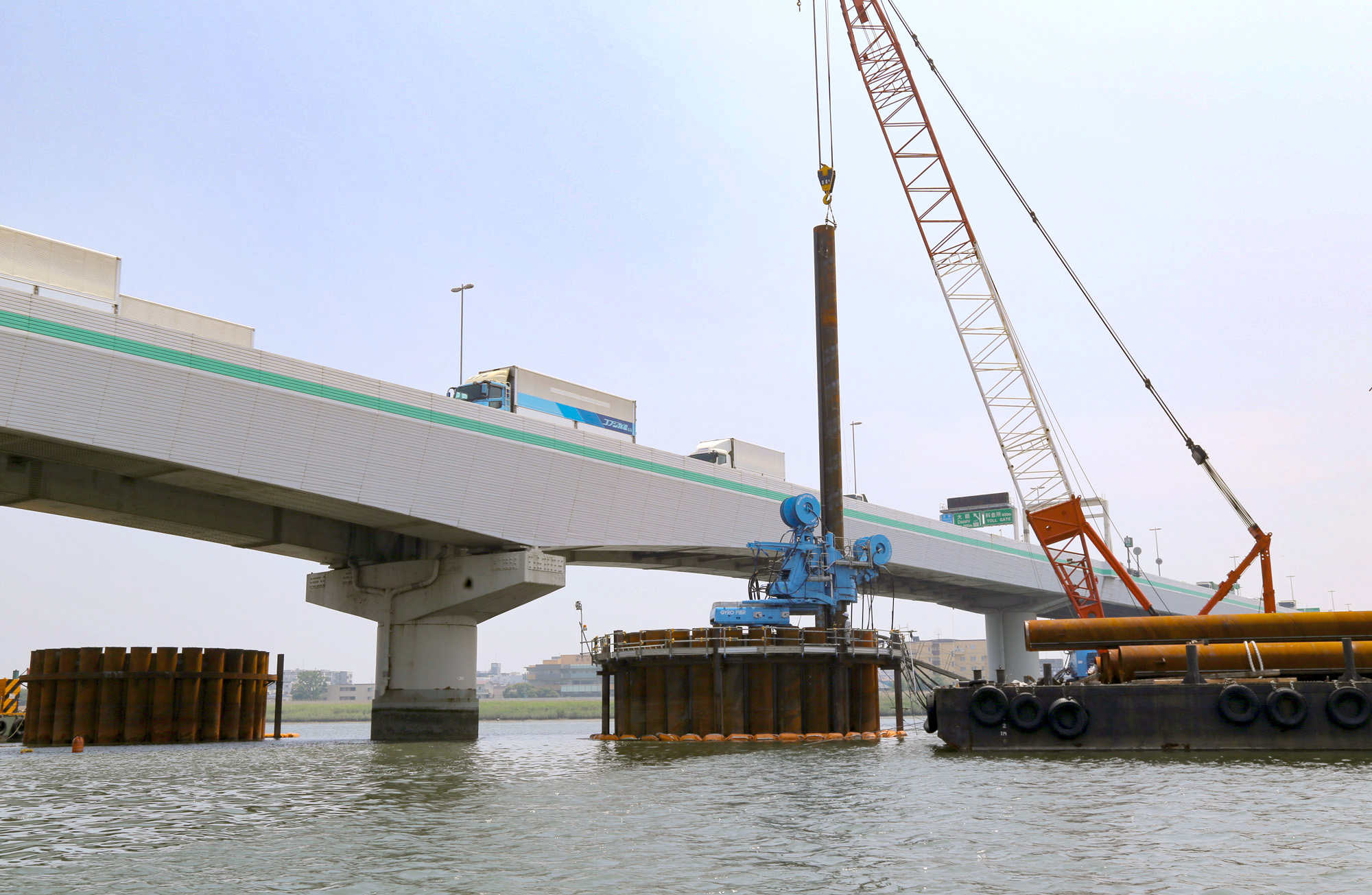
■Overview of the Daishi Expressway Bridge Renewal*
The Shutoko was first opened in 1962, but increasing age and traffic volumes have caused damage to worsen. This is why the Shutoko Renewal Project is underway to completely replace its roads and bridges.
Daishi Expressway Bridge, which was opened in 1968, carries some 80,000 vehicles daily between Tokyo and Kanagawa, but cracks were identified in more than 1,200 locations on it. The replacement work involved constructing new piers, then sliding a new pre-assembled girder section over the existing girder section to replace it all at once. This innovative method shortened the time the bridge was closed to traffic to two weeks, drawing attention.
* Reference: Metropolitan Expressway Co., Ltd. website (https://www.shutoko.jp/ss/daishibashi/)
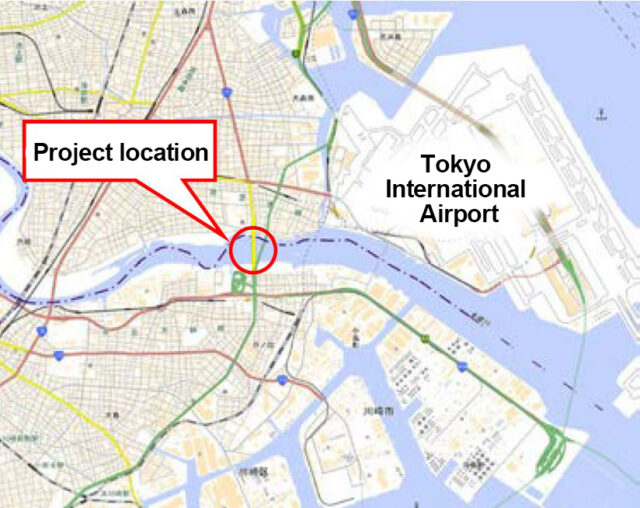
Prepared by GIKEN LTD. based on Fundamental Geospatial Data
(provided by Geospatial Information Authority of Japan)
(https://fgd.gsi.go.jp/download/menu.php)
■Construction Details
Tubular sheet pile pier foundations for P4-6 piers were constructed. Our GRV1230 (SP12) pile press-in and extraction machine, which can handle 1,000 mm-diameter tubular sheet piles, was used to press in a total of 192 tubular sheet piles ranging in length from 49 to 53 metres.
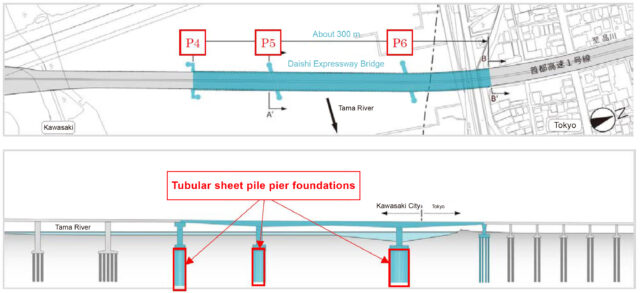
Prepared by GIKEN LTD. based on data supplied from Metropolitan Expressway Co., Ltd.
■Reason for Adoption
Press-in that allowed high precision to be maintained even for long piles
Normally, the longer the pile the more difficult it is to maintain precision, but the SILENT PILERTM pile press-in and extraction machine we manufacture and sell grips the pile low, near ground level, to press it in, so the down-stroke power is properly transmitted to the pile, making it harder for the pile toe to change position. These advantages allowed the construction of foundations with high precision.
Safe, quick construction with no effects on traffic
To maintain traffic flows on the Daishi Expressway Bridge right next door, even during construction, it was necessary to ensure high safety levels and complete work quickly. The SILENT PILERTM not only grips driven piles firmly but grips the new piles not at the top but near the middle, ensuring physical stability for both machine and pile without the risk of toppling over. In addition, the pressed-in piles are held strongly through hydraulic pressure, ensuring that even long piles will not wobble and come into contact with the bridge. Also, being able to carry out work through being self-moving atop driven piles means that there is no need for the large temporary bridges required by other construction methods that employ large machinery, meaning that installation and removal work are not required. The extremely high construction safety levels and simple process mean that work can be done speedily, without affecting traffic.
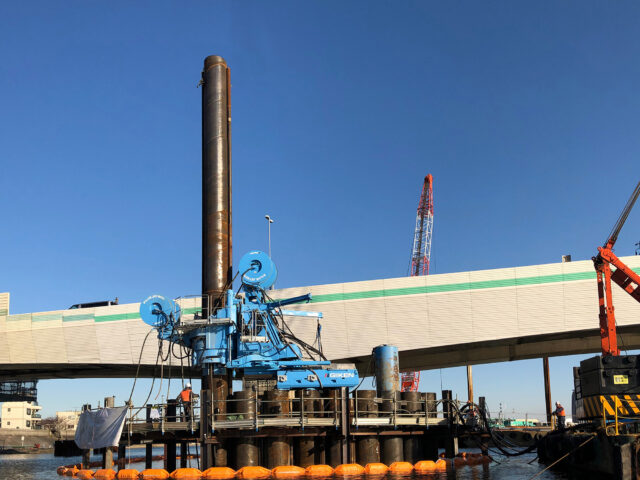
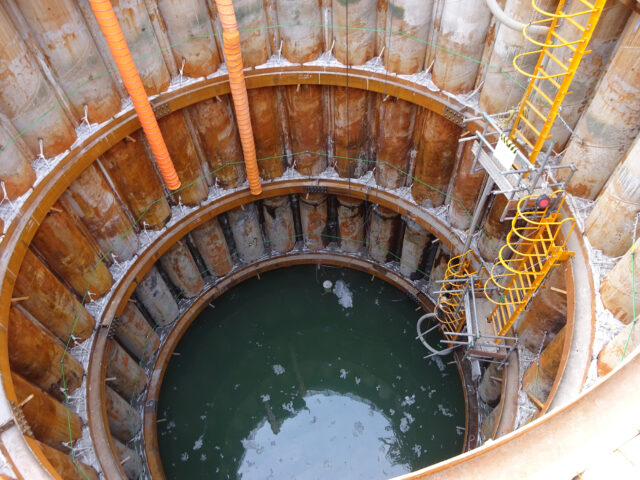
Project Name | Daishi Expressway Bridge Renewal Project |
---|---|
Location | Haneda area, Ota-ku, Tokyo |
Project Owner | Metropolitan Expressway Co., Ltd. |
Prime Contractor | TAISEI CORPORATION, TOYO CONSTRUCTION CO., LTD., IHI Infrastructure Systems Co., Ltd. and Yokogawa Bridge Corp. (joint venture) Sub-contractor: GIKEN SEKO CO., LTD. |
Sub-contractor | GIKEN SEKO CO., LTD. |
Equipment | GRV1230 (SP12) |
Specification of Pile Elements | P4: 88 tubular piles (diameter 1,000 mm, length 49.5 m, PP joints) P5: 56 tubular piles (diameter 1,000 mm, length 49.0 m, PP joints) P6: 48 tubular piles (diameter 1,000 mm, length 53.0 m, PP joints) |
Press-in Construction Period | April 2018 to April 2019 |
■Profile of GIKEN Group
GIKEN developed SILENT PILERTM, the world’s first reaction-based hydraulic pile jacking machine, installing piles without noise or vibration. GIKEN Group now actively promotes its press-in technology worldwide and contributes to the construction industry by proposing and implementing innovative solutions. The innovative press-in technology provides a unique solution and the adoption of this technology has spread to over 40 nations and regions.
Contact Us