GIKEN LTD. (Head Office: Kochi, Japan; President: Shinnosuke Moribe) has developed a GYRO PILERTM ※1 rotary cutting press-in machine for tubular piles with ultra-low overhead clearance (patent pending). Use of existing GIKEN press-in machines was not feasible in hard-ground locations with only 2.5 meters of headroom, including around aging bridges in urban areas. The new machine enables press-in installation of tubular piles with a 1,000-millimeter diameter.
Improvements to the machine’s rotary mechanisms dramatically lower the minimum overhead clearance for works to 2.5 meters compared to the 4.5 meters required for the existing Low-Headroom GYRO PILERTM. Work efficiency is also significantly improved by the ability to pitch longer piles as this reduces both the number of piles used and the number of welded joints during joining work※2. The new machine offers a revolutionary solution for projects stymied by a combination of severely restricted headroom and hard ground, such as seismic strengthening of bridges and reinforcement of river revetments around bridges. It will contribute to national resilience—for example, by ensuring transport route availability after a destructive earthquake—as well as longer-lasting infrastructure and a sustainable society.
The machine will initially be introduced to work sites of group company GIKEN SEKO CO., LTD. (Head Office: Kochi, Japan; President: Akihiro Nishigawa) to rack up performance in the field and undergo improvements before introduction to the market. For GIKEN, the new model is an opportunity to further develop avenues in a sector where the GIKEN Group has a competitive edge—the press-in market—and thereby bring about higher sales and profit for the GIKEN Group and, by extension, users.
※1 A press-in machine designed specifically for the Gyropress Method™ of rotary cutting press-in installation of tubular piles. Tubular piles with cutting teeth attached are rotated as they are pressed in, allowing them to penetrate hard ground and concrete or other obstacles in the ground and create a robust and resilient implant structure.
※2 Work involving the welding or other joining together of short piles when headroom limitations restrict pitching of long piles
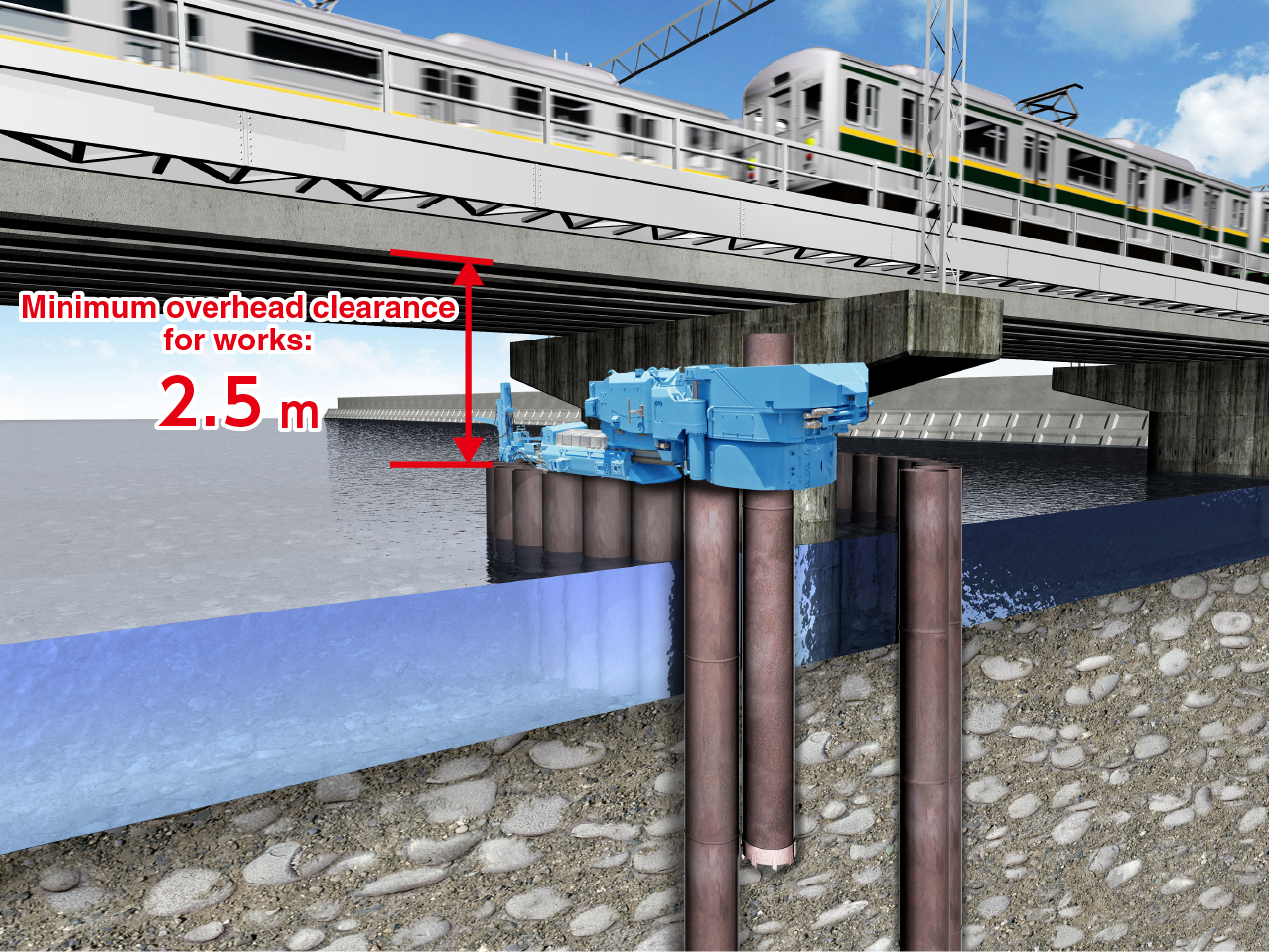
Illustration of the Ultra-Low-Headroom GYRO PILER™ at work *Colors differ from the actual machine developed.
■ Streamlining Construction of Underwater Tubular Piling
[Horizontal pile feeding from the side of the machine]
➢Earlier models required pile feeding from above using a hoisting device
Earlier machines had an integrated hoisting device for lifting piles up and inserting them into the machine from above. This required a certain amount of clearance to avoid interference with overhead obstacles.
➢The new model allows pile feeding from the side
The new machine’s design allows 90-degree rotation of leader mast※3 and chuck※4, enabling horizontal feeding of piles into the machine from the side using a special-purpose pile-feeding device in place of a hoisting device. This lowers the overhead clearance required for works. Because longer piles can be pitched, fewer piles are used and fewer joints are welded during joining work, reducing work cost and duration.
※3 Component that guides down and up strokes and determines lateral positioning of the pile to be pressed in
※4 Component that clamps the pile to be pressed in
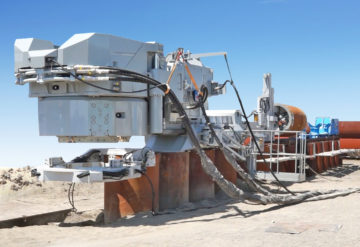
(1) Normal position
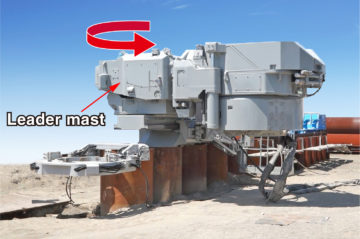
(2) Leader mast swivels 90 degrees
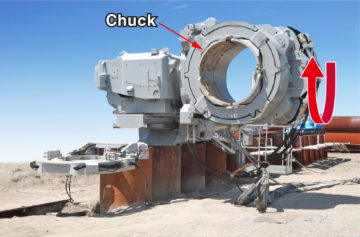
(3) Chuck rotates up 90 degrees
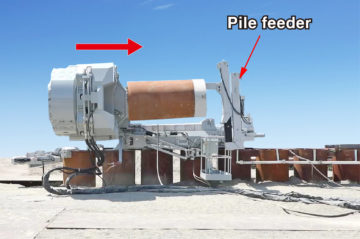
(4) Pile is introduced
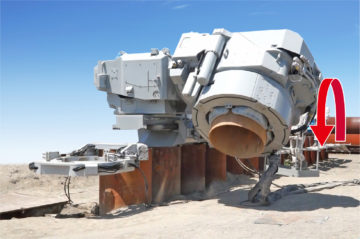
(5) Chuck rotates back down 90 degrees
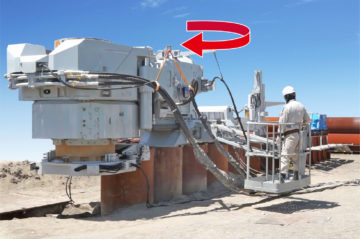
(6) Leader mast swivels back and pile feeding is completed
[Automatic Return to Pile Feed Position]
A new feature for automatically returning the machine to pile feed position is included. Manually adjusting the machine to prepare for pile feeding can result in operation and judgment delays. Instead, the process is efficiently performed with a single button, reducing the burden on operators.
■Comparison with Earlier Model
▶Lowering the minimum overhead clearance for works dramatically expands the scope of potential projects.
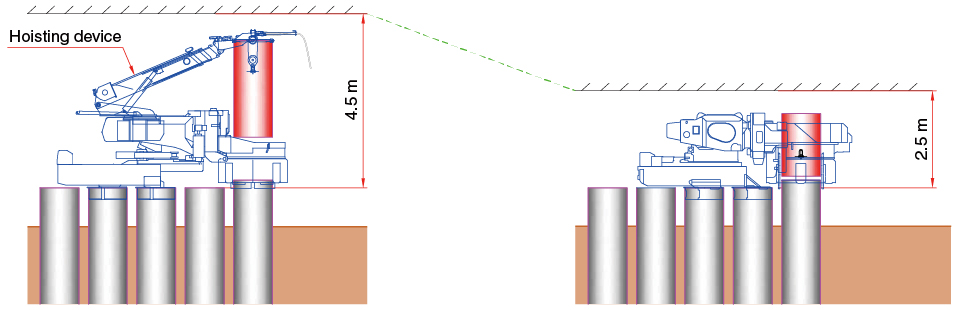
Left: Earlier Model Right: New Model
▶Longer piles can be pitched, reducing the number of joints
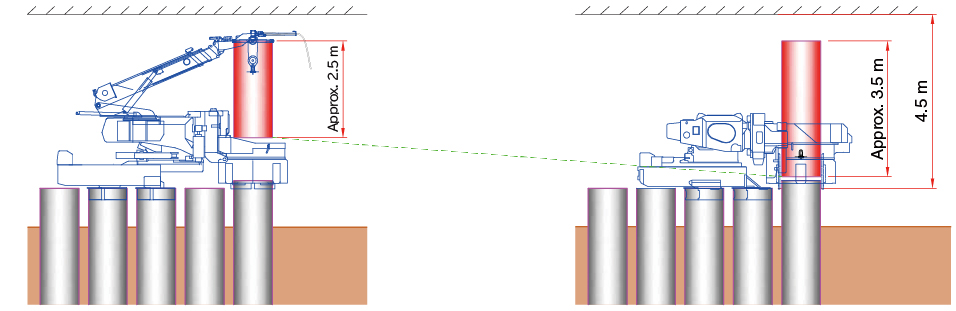
Left: Earlier Model Right: New Model
■Outlook and Expectations
With the new machine, it is no longer necessary to dismantle bridge girders or put in place detours even where the ground is hard and headroom is severely restricted. Work underneath bridges and foundation reinforcements are easily carried out without impacting surrounding transport or the regional economy. Amid talk of national resilience and longer-lasting infrastructure, inquiries about low-headroom projects are expected to increase and buyers have suggested the Ultra-Low-Headroom GYRO PILERTM, allowing overhead clearance down to 2.5 meters, would enable swift action. Expectations for the new machine are high.
■Basic Specifications
Applicable piles | Tubular piles (φ1,000 mm) |
Press-in force | 1,500 kN |
Extraction force | 1,600 kN |
Max. rotation torque | 600 kN・m |
Max. rotation speed | 12.0 min-1 |
Chuck up/down stroke | 700 mm |
Rotating press-in speed | 0.8 – 6.3 m/min |
Rotating extraction speed | 0.6 – 4.7 m/min |
Min. overhead clearance for works | 2,500 mm |
Mass of press-in machine main body | 25,550 kg |
■Profile of GIKEN Group
GIKEN developed the SILENT PILERTM, the world's first reaction-based hydraulic pile jacking machine, installing piles with no noise and vibration. GIKEN Group now actively promotes the Press-in Technology worldwide and contributes to the construction industry by proposing and implementing innovative solutions. The innovative technology of press-in provides a unique solution and the adoption of this technology has grown to more than 40 nations and regions.
GIKEN LTD.
International Business Department
TEL: +81-3-3528-1633 (weekdays: 8:30 to 17:30)
Tokyo Head Office: 16F Ariake Central Tower, 3-7-18 Ariake, Koto-ku, 135-0063, Japan